Course info
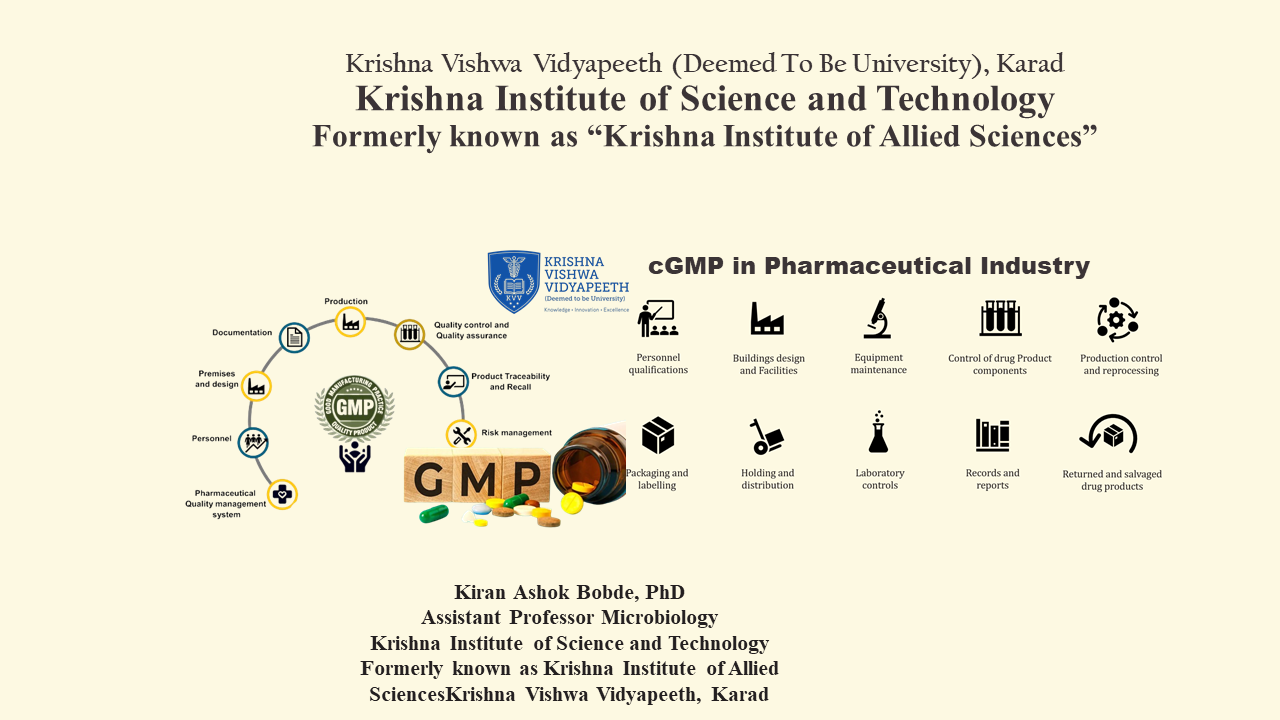
Current good production practice (CGMP) is the necessary rules in the pharmaceutical industry designed to ensure protection, quality and effect of medicines. They control all aspects of production, from the benefits of personnel to design and maintenance of equipment, and ensure that products meet regulatory standards and are free of pollution. CGMP product is important for maintaining integrity, preventing errors and protecting patient health. Common challenges in following CGMP standards include inadequate documentation, cross provisions, insufficient employee training and malfunction in the tool. These problems can have serious consequences, including regulator penalties and compromise product quality. The solution of solving these challenges involves implementing strong documentation systems, integrating advanced quality control measures, providing continuous training of employees and taking advantage of modern technology such as automation and real -time automation and surveillance systems, CGMP's primary targets include frequent product quality, reduction of pollution, protection, protection, protection and increasing reputation. Important CGMP exercises cover organizational structure, personnel training, convenience design, equipment maintenance, raw material control, production process monitoring and quality assurance. Facilities should be designed to prevent contamination, the unit must be calibrated regularly, and strict hygiene protocols should be followed. In addition, appropriate record keeping, packaging and storage practices are necessary to maintain compliance. By following CGMP, pharmaceutical companies ensure product safety, regulation compliance and consumer confidence.
- Teacher: Dean KIST